Search results - "treadle" |
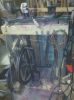
hook3.jpgcrochet hook extender28 viewsthe treadle lathe and chuck nicknaylo
|
|
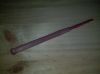
hook1.jpgcrochet hook extender22 viewsin purpleheart, turned on the treadle lathe. nicknaylo
|
|
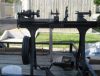
barnes_lathe1.jpg61 viewsF.W. Barnes treadle powered metal lathe in perfect condition. The bucket at the bottom left and 2 boxes were full of the tooling, change gears, etc for the lathe. It even had the cast iton seat.galootgary
|
|
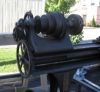
Barnes_lathe_headstock.jpg43 viewsF.W. Barnes treadle powered metal lathe headstock, showing change gears for thread cutting. The brass plate at the lower center lists what gear combination would cut what pitch of threads.galootgary
|
|
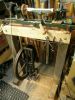
first.JPGTreadle lathe version 3,maybe 3.4208 viewsself contained flywheel, construction lumber frame, 30's era lathe, rope drive belt. nicknaylo
|
|
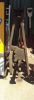
Chapman_movable_forge.JPGChapman No. 6 Portable Forge Treadle Grinder160 viewsFound this at an antique shop while searching for LOML's birthday present.OldSneelock
|
|
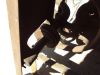
Chapman_Movable_Forge_Treadle_Grinder_Clutch.JPGTreadle Grinder Clutch101 viewsFrom the looks of the layout there was a strap attached to the two screws on the left hand hub of the clutch. When the pedal is pushed down the strap unwinds causing the clutch to engage and rotate the shaft and large flat belt pulley. When the pedal is released the clutch ratchets back and resets for another pulse.
OldSneelock
|
|

old_bench.jpgOld bench103 viewsOld bench, became a treadle lathe, now holds lathe chisels and other stuff. Base is an old treadle sewing machine. In front is my sawbench.Bad Andy
|
|
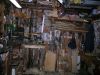
image0001~2.jpgEast Wall155 viewsTreadle lathe, post drill, neaderbuddy and lumber racknicknaylo
|
|
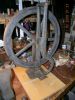
flywheel_cleaned.JPG21 inch pedal flywheel141 views64 lbs, marked only Patented April 14, 1898. the start of Treadle Lathe Concept #3nicknaylo
|
|
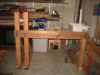
Lathe_1.jpgFull view of lathe90 viewsThis is early in the build, before the flywheel, headstock, treadle, etc.. was completely done.Sam Peterson
|
|
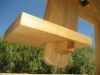
IMG_0208.JPGJoinery - Treadle151 viewsSlightly non-standard tusk-tennon since the main mortise and tennon cheeks are at an 80 degree angle to the arm, so the tusk has to have its bearing face cut at that angle too.TRexF16
|
|
20 files on 2 page(s) |
 |
1 |  |
|